Moldflow
Product
Design, Inc. uses Moldflow products to improve the moldability of our
plastic part designs. Most molding problems are a byproduct of the plastic
part design itself. Since molding problems do not present themselves until
after the mold is built, fixing these problems is usually costly and always
causes considerable delay. By using a tool like Moldflow during the part
design phase we can greatly reduce the chances of molding problems later
in the project. Moldflow cannot turn a bad injection mold into a good
injection mold, so it must be used during the part design phase for maximum
benefit.
.
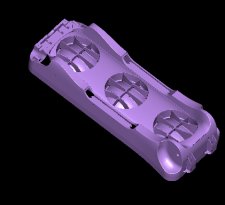
Moldflow
as a design check
The common usage of moldflow is as a design checker that is used
as a part is nearing completion. As plastic part designs get more complex
it is more difficult to predict the performance of the part as it is being
molded or even if the part can be molded. Moldflow can improve your confidence
in mold fill, sink marks, warp and knit lines prediction and therefore
reduce the risk of molding problems that are a byproduct of the part design.
Moldflow
as a conceptual tool
Our
favorite use of Moldflow is as a concept development tool. All good designs
are based on one or more strong concepts. Just as a strong appearance
or structural concept can be the key to turning a good idea into a functional
product, a good plastic flow concept can turn an unmoldable problem part
design into a cost effective, easy to mold part.
Product
Design, Inc.
5100 Main St. LL102
Downers Grove, Illinois 60515
Phone: 630.663.1642
Fax: 630.663.4552
info@pro-des.com
Home
| Product
Development | Concepts
| Engineering
| Moldflow
Plastic
Part Design | Pro/Engineer
Surfacing | Solidworks
Plastic
Design Temps
| FEA
Stress Analysis | IGES
| Gallery
|